
Industry
Aerospace Manufacturing
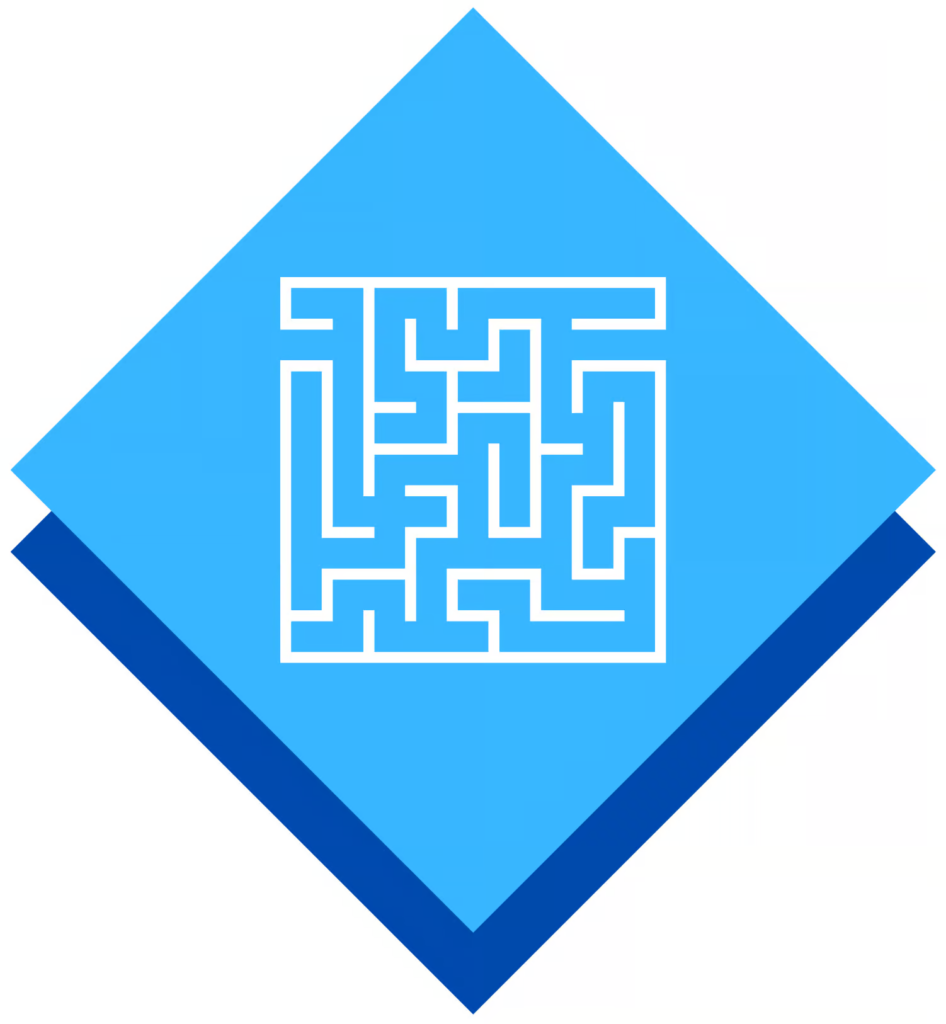
Challenge
Heat Distribution, Chemical Resistance
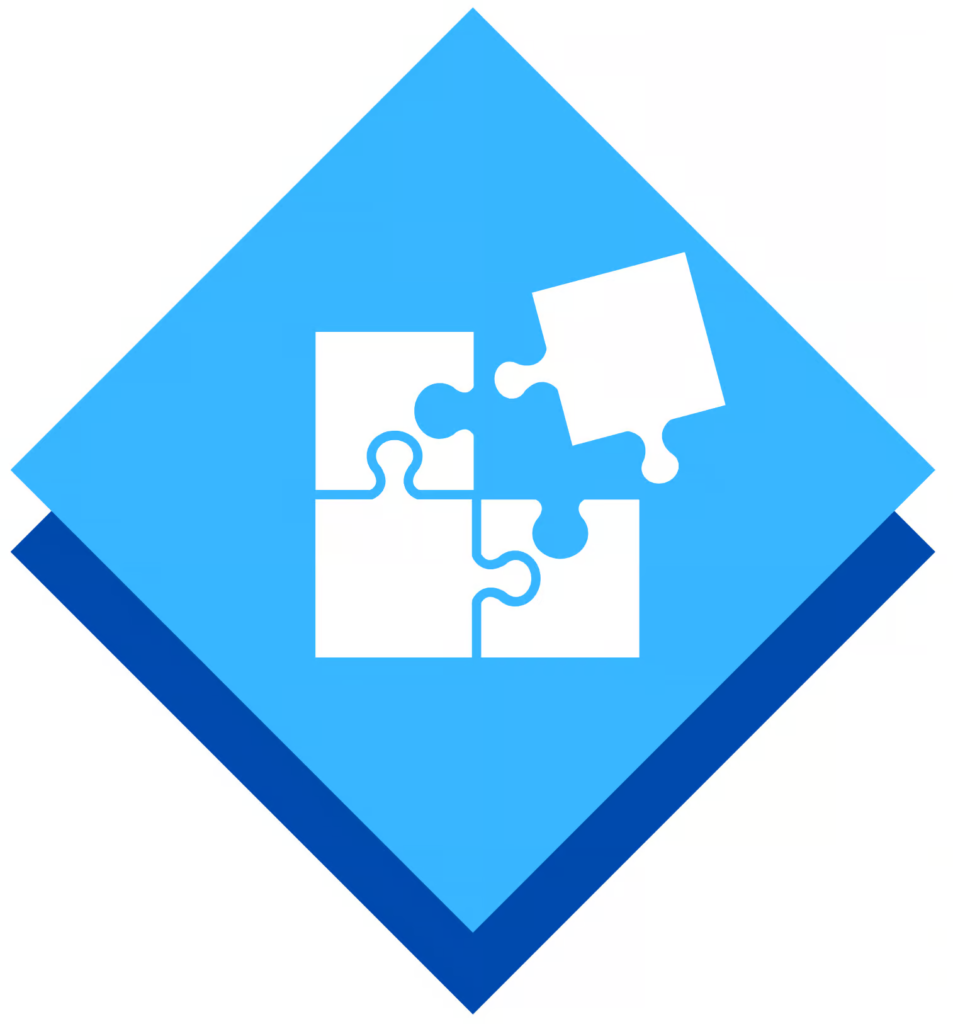
Solution
Manganese Phosphate Tank Assembly
Burt Process Equipment developed a 170-gallon manganese phosphate tank assembly tailored to the client’s specific needs. The system included:
- Double-Walled Stainless Steel Tank: Built with 316 stainless steel, the 170-gallon tank (33” x 33” x 36”) featured a 5-inch-wide glycol-filled jacket for even heat distribution. This tank’s construction offered superior corrosion resistance to withstand the harsh phosphate coating environment.
- Efficient Heating System: The system incorporated four flange-mounted electric heaters (26” immersion length) into the glycol jacket, with the heaters made of stainless steel for durability. The heaters were controlled by a sophisticated temperature control panel to maintain the solution at the optimal 190-210°F (88-99°C) required for the phosphate coating process.
- Glycol Recirculation: A Finish Thompson AC Series centrifugal pump (30 GPM) provided efficient glycol recirculation to ensure uniform heat across the tank’s surface, crucial for maintaining consistent coating quality.
- Exhaust Hood: Rear double-slot PVC welded exhaust hood for fume removal and tie-in to customer’s existing exhaust system.
- Conductivity Level Monitors: Two conductivity level monitors were installed to prevent overfilling and ensure proper fluid levels, automatically shutting off the heaters if levels dropped too low, safeguarding the system.
- Advanced Control Panel: The control panel, rated NEMA 4X and UL-listed, featured a temperature controller, recirculation pump control, and alarm systems for monitoring temperature and fluid levels. Safety features like an alarm horn with pushbutton silence for out-of-range conditions ensured operational reliability.
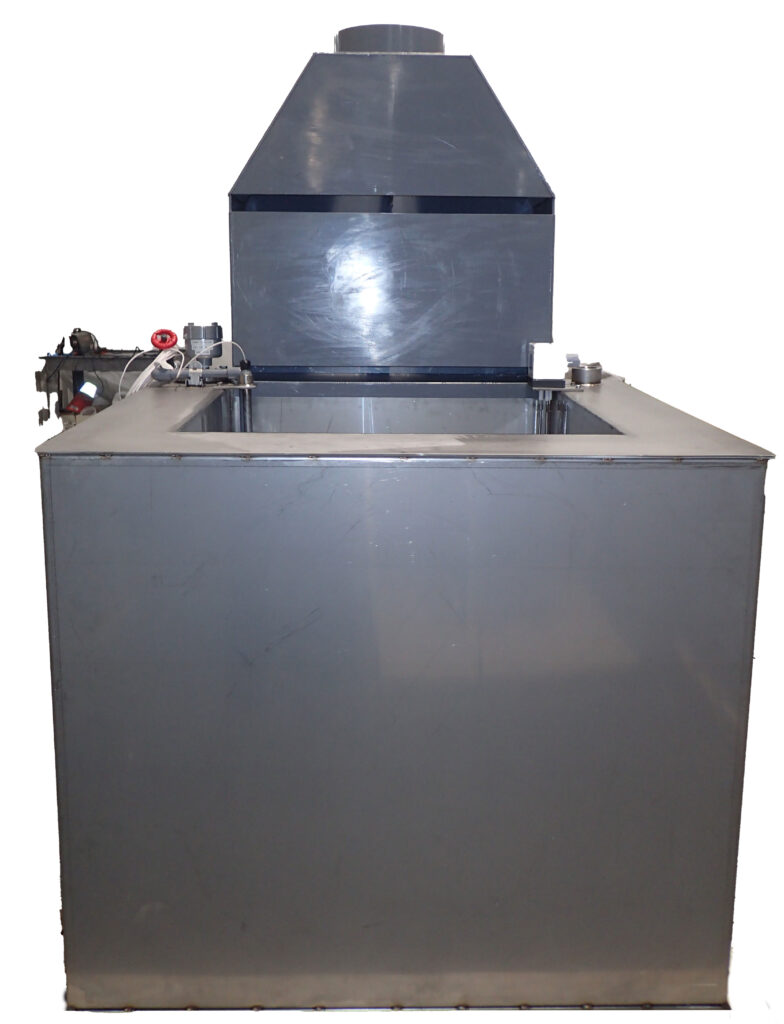
Manganese Phosphate Coating Process
Manganese phosphate coating is a vital process that forms a crystalline layer on metal surfaces, providing enhanced wear resistance, corrosion protection, and excellent oil retention properties. This treatment is ideal for aerospace applications where components are subjected to high stress. The process involves several stages:
- Cleaning and Degreasing: Metal parts are cleaned to remove contaminants, ensuring a uniform coating.
- Activation: An acidic solution prepares the surface for better coating adhesion.
- Phosphating: Parts are immersed in a heated solution of manganese and phosphoric acid, where the manganese chemically bonds with the metal surface.
- Rinsing and Drying: Parts are thoroughly rinsed and dried to remove any remaining chemicals.
- Post-Treatment: In some cases, an oil coating is applied to enhance corrosion resistance and lubrication properties.
Results
The Burt Process Equipment manganese phosphate coating system met the client’s needs for precision and reliability. It ensured uniform coating thickness, enhanced wear resistance, and reduced the need for frequent maintenance. This solution significantly improved the durability of the aerospace components, reducing downtime and ensuring compliance with industry safety and environmental standards.
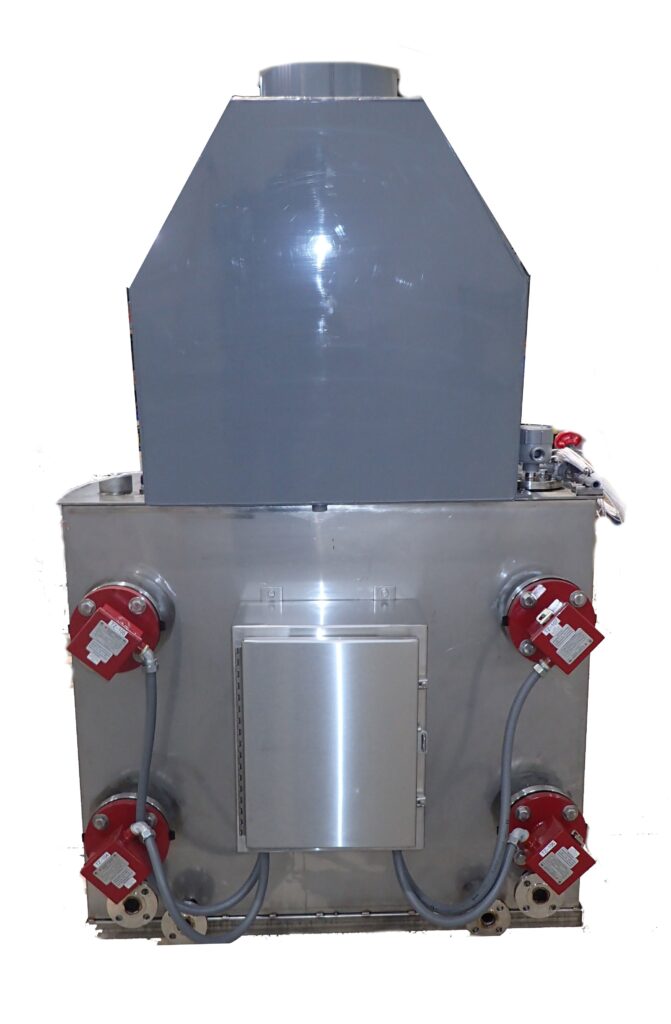
Do you have a similar application?